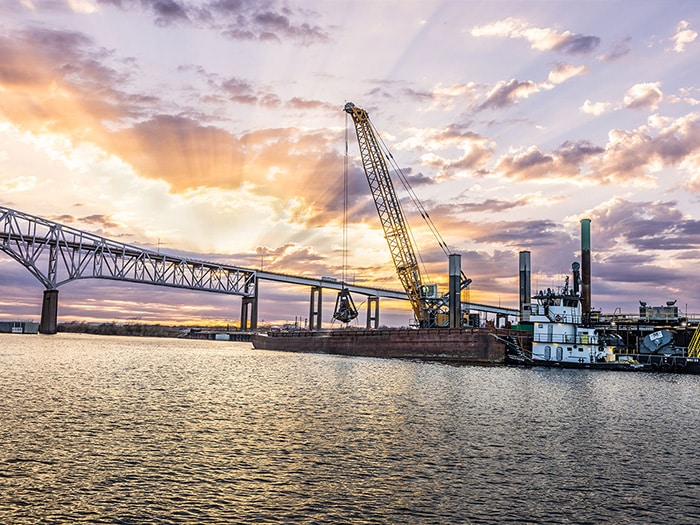
Matthews Brothers Inc. is utilizing a Liebherr HS 8300 crawler crane on a Port Arthur, Texas, undertaking.
The Liebherr Group experiences that two of its clients are placing its HS 8300 responsibility cycle crawler crane to the check on two large-scale U.S. Gulf coast dredging initiatives which are 350 miles aside.
In Port Arthur, Texas, Matthews Brothers Inc. is engaged on a good deadline on the port aiding in new development off of an present dock. The Pass Christian, Miss., headquartered firm makes use of a Liebherr HS 8300 with 8.5 yd TGS clamshell bucket to dredge over 5000 yards of onerous clay, sand, and particles per day.
In Mobile, Ala., the San Rafael, Calif., based mostly Dutra Group is using a personalized HS 8300 responsibility cycle crawler crane on a deepening undertaking on a Corps of Engineers undertaking
Every jobsite comes with its challenges. In Port Arthur, Matthews Brothers is dredging 46 ft deep in a basin, the place the onerous sediment is especially difficult to maneuver. The machines should be capable to deal with strenuous work over lengthy durations of time. However, says Liebherr, its HS 8300, one of many largest responsibility cycle cranes on the planet, is designed for an prolonged service life supreme for dynamic purposes, equivalent to dredging.
On this undertaking, Matthews Brothers is using Liebherr’s dredging assistant bundle on its HS 8300. The assistant permits the machine to preset the opening and shutting parameters for every bucket making grabbing simpler and extra environment friendly. The end result permits for longer lifetime of the cables and reduces basic put on and tear on the bucket.
“The overall impression shared throughout the company is how simple the HS 8300 is to use, allowing us to work faster, have higher productivity, and meet the deadline of the customer,” notes Matthews Brothers dredge captain, Alex Kellams. “Using the HS 8300 allows us to get in and out quicker and provides a smoother dredging operation, so it’s a win-win situation for everyone.”
To enhance productiveness, the corporate makes use of the Liebherr Pactronic hybrid drive for the responsibility cycle crane. This is is a further power storage system. If extra power is required for crane operation, the Pactronic system transfers the power saved within the accumulator again into the system, enhancing the dealing with efficiency of the crane.
“Pactronic is much faster and allows us to move twice as fast resulting in quicker load and cycle times as well as promoting fuel efficiency,” says Kellams.
Keeping to a strict deadline, Matthews should maintain the undertaking shifting because the port continues to function. The machine runs 20 hours a day and downtime might be very pricey, so help from Liebherr is significant on the subject of servicing the machine. “
“We got the Liebherr because of the backing they offer. We don’t have to diagnose any problems on our own,” Kellams notes. “We have the help from Liebherr to get us through any problems we might have.”
Matthews Brothers belief in Liebherr stems from the corporate’s previous purchases of an LH 80 materials handler and HS 8200 responsibility cycle crane that now operates subsequent to HS 8300.
Many clients respect the convenience of transition is from one Liebherr machine to a different, together with the Dutra Group, which is using a personalized HS 8300 on the Alabama peoject. Working on section 4 of six, the crane is mounted on a barge, dredging at a depth of 54 ft on the Mobile channel deepening undertaking.
“We have utilized the LR 1300s and the 895, so when you get into a brand-new machine the controls are very similar,” says Dennis Ferguson, fleet supervisor for the Dutra Group’s clamshell division. “It was a short period between accepting the crane, getting it on the barge, and going to work.”
Dutra analyzed a number of price efficiency research and analysis earlier than buying the HS 8300 and is glad with its 65 second cycle instances per swing, averaging 10,500 cubic yards per day.
“We have been watching production pretty close,” says Ferguson. “The cycle times were right where we projected.”
Additional customization of the Dutra HS 8300 consists of implementing crawler tracks reasonably than a pedestal mount for simpler transport, in addition to a wider, raised cab, larger winches, and a lighter growth.
“Dutra relies on Liebherr sales and factory representatives to make sure whatever upgrades and customizations we do fit into our specifications and individual needs,” notes Ferguson. “These customizations provide us with versatility and increased production and efficiency.”
The HS 8300 is at present Liebherr’s largest manufacturing dredging machine. The responsibility cycle crawler crane is supplied with a 1,000 hp EPA Tier 4 remaining engine in addition to the Pactronic resolution which offers roughly 1,500 hp to help the 154,000 lb sign line pole winches.
“The big horsepower and big winches make this ideal for our U.S. customers,” says Liebherr Sales Manager Steve Whisenhunt. “This machine is capable of doing over 4 million cycles which is a very strong spec for this class of machine.”