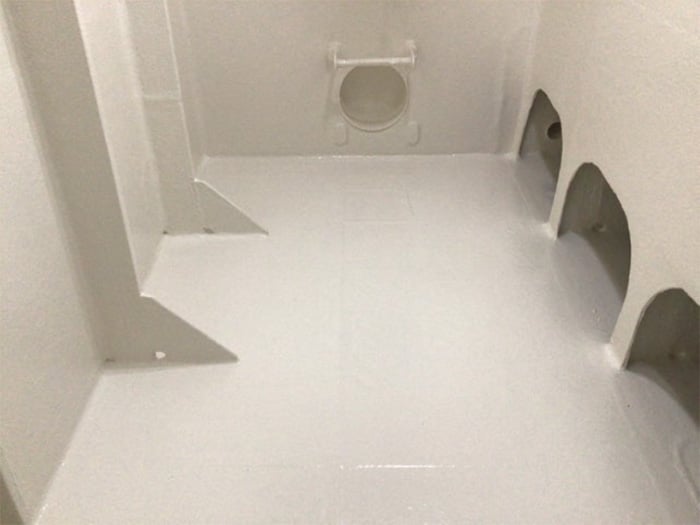
Open-loop scrubber tank of Vulkan Materials’ self-discharging bulker after recoating with Tnemec system
Exhaust gasoline scrubber techniques aren’t all the time problem-free and when America’s largest producer of development aggregates, Vulcan Materials Company, encountered coatings points with the scrubber system tanks within the 2018-built, 66,445 dwt self-discharging bulker Donald M. James it reached out to a specialist, Tnemec Company Inc., for an answer.
Vulcan makes use of the Bahamas-flagged Donald M. James to move limestone combination between Mexico and the U.S. Gulf Coast and opted to adjust to the IMO 2020 sulfur limits by becoming the ship with a scrubber. To shield the scrubber system’s tanks, a pin-hole-free, high-performance lining, was required.
When the unique coatings techniques on the scrubber tanks skilled early failures, Vulcan Materials knew one other resolution was wanted. With the assistance of Wilhelmsen Ship Management (WSM), the crew got down to discover the proper coatings system for the job and reached out to Tnemec and the native company in Alabama, SteelCon Coatings Systems.
SteelCon was in a position to work with WSM to shortly present a challenge specification for the vessel’s tanks within the quick time-frame the ship was docked. Understanding the urgency and realizing most vinyl ester coatings are “made to order,” Tnemec was in a position to pace up the manufacturing timeline to assist the Donald M. James get off the dock and again to work.
The specification included an entire vinyl ester system utilizing Tnemec Vinester 1407, 1436, and 1416. The crew additionally added fiberglass chop strand mats to areas that sometimes see coating failures for added safety.
“We made sure to have a Tnemec NACE certified coatings inspector onsite throughout the duration of the application of the first tank to ensure the coatings were applied to specification,” stated Andy Margarit, gross sales director, marine, at Tnemec. “The vessel captain, WSM, TAM Services, and Tnemec worked together to apply the extremely technical system, all while navigating the small confines inside the tanks. It was quite a feat.”
First, Tnemec VInester 1407 was utilized on the tank welds after which a full coat of 1407 was utilized to the complete tank. Next, a coat of Tnemec Vinester 1436, a premium grade novolac vinyl ester with glass flakes within the lining was utilized at 25-30 mils and instantly embedded with a corrosion-resistant fiberglass chop strand mat. The reinforcing mat was wetted with Vinester 1416, a pure novolac vinyl ester, referred to within the enterprise as a saturant coat. A coat of 1436 at 25-30 mils was then utilized three toes up the bulkheads and the ground was accomplished with the coating/mat and saturant system. To end the tanks, 1436, in a vibrant white end, enhancing visibility within the enclosed house, was utilized over the complete floor as the ultimate protecting layer.
The challenge took a complete of two weeks to finish. Within that point, greater than 400 gallons of made-to-order high-performance coatings have been put in on the scrubber tanks. Despite the challenges many coatings corporations have been dealing with in supplying vinyl ester techniques, Tnemec was in a position to ship the coatings straight from the manufacturing plant in Kansas City to the ship docks in Mobile, Alabama, avoiding delays in freight transit time. This saved the challenge on observe permitting the vessel to go away the port on time.